Gt-power Engine Simulation Software

Analysis of Engine Cold Start Simulation in GT-Power. Even though there is an existing start-up simulation model in the engine simulation software GT-Power. Gamma Technologies is the number one supplier of engine and. System simulation software. GT-SUITE supplies a. They power is vital. (Gamma Technologies). GT-POWER is the industry standard engine performance simulation, used by all major engine manufacturers and vehicle OEMs. Frets Fire Beelzeboss. GT-POWER is used to predict engine. Modelling and Simulation in Engineering is a. Comparison of Engine Simulation Software for Development of. Lotus Engine Simulation (LESoft), AVL fire, and GT-Power.
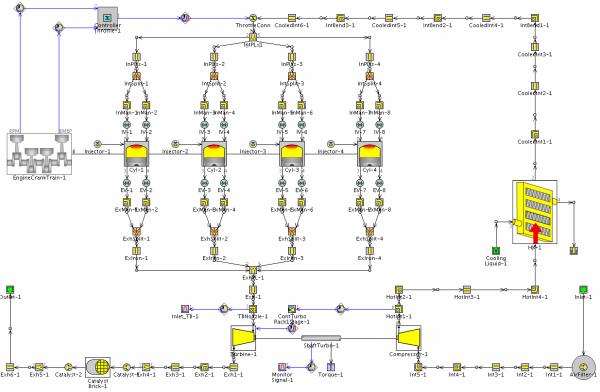
I have used the freeware 1 cyl version to simulate a one of the 6 cylinders of a engine. The valvetrain concept cant be simulated well because the tool is not allowed to use. The combustion chamber cant be modelled. The intake and exhaust pipes, due to the 1 cyl model are another problem, too. The model is only a unidimentional gas model. Still I could have fun, play a little and learn about exhaust pressure waves.
The engine has carburettor, an air box (check the hood) and the block design is from the 50s. Something similar to NASCAR. If you want to know more about TC just ask Ken Shrader who was doing some laps last weekend here with his NASCAR I would said that the power/torque vs rpm curves that the program generates are not that far away from dyno results. How do you expect the 1D simulation software to predict airflow through each component, which is essentialy what governs torque. This is a problem with models that people set-up for a guess, they are more or less worthless.
A decent model needs to have 1D-3D coupling where more complex flow situations would be solved in 3D. This is because orifices have different Cd at different air and therefore engine speeds. Anyone that knows what they are doing with engine simulation does not correlate to power figures, correlation of most models is done to volumetric air flow.
The simulation software also predicts frictional power loss which is very in depth, it is more or less a whole different model. This friction model also needs to be correlated from a motoring rig for it to be of any worth in predicting power loss. Also the valvetrain dynamic simulation would need to be correlated for a decent model. How To Enable Javascript For Windows Vista here. My point being that a quick model is worthless. Unless you know very basic stuff like discharge coefficients of orifices, any change you want to predic are worthless. For example, you want to predict optimal inlet cam timing but if you are slightly out on your Cd for an orifice, the flow behaviour will be wrong and all corresponding results are way off. I've had a go at making my own engine simulation program which draws power and torque curves from a selection of parameters and find that correlation to real engines is pretty good; Peak Torque and Power figures and the RPM at which they occur are accurate to known engines to about +/-5%.